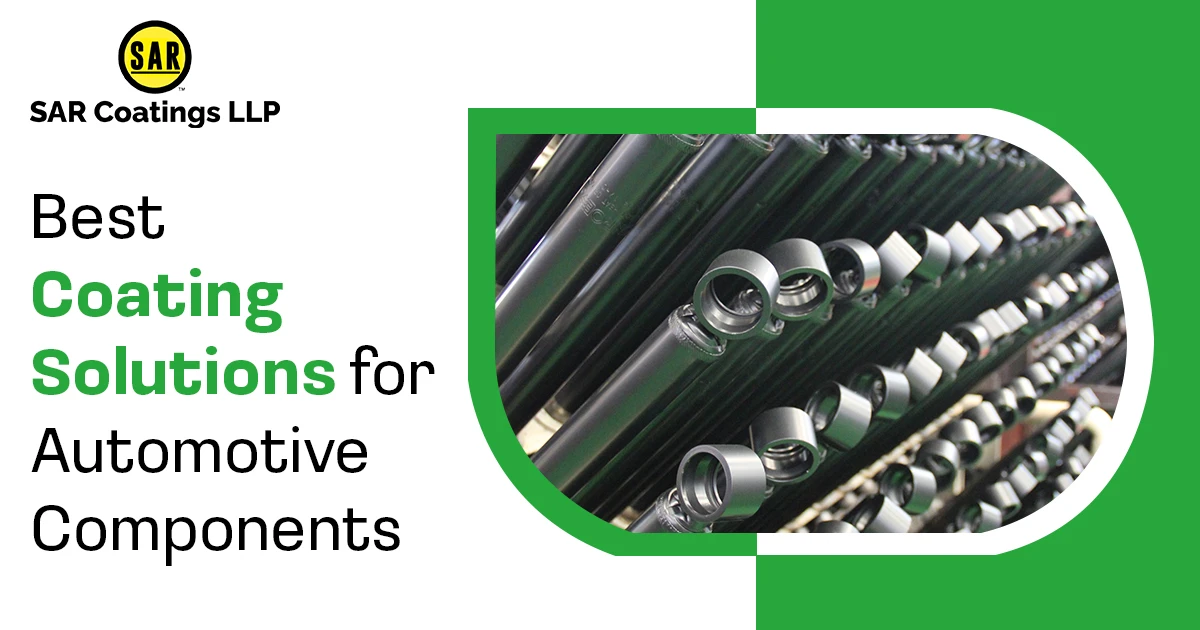
Best Coating Solutions for Automotive Components in 2025
In the automotive world, durability isn't a luxury; it's a requirement. Every bolt, bracket, and body panel faces constant stress: road salt, vibration, temperature shifts, chemicals, moisture, and more. The difference between a failed part and a high-performing vehicle? Often, it's the coating.
At SAR Coatings, we work closely with OEMs, Tier 1 suppliers, and component manufacturers to deliver coating solutions that go beyond aesthetics protecting, extending lifespan, and enhancing performance in real-world driving conditions.
Here’s a closer look at the top coating technologies trusted by the automotive industry in 2025, and how SAR Coatings ensures your parts meet the standards of modern mobility.
1. Powder Coating: The Backbone of Surface Protection
Used for: Chassis parts, suspension components, wheel hubs, underbody elements
Why it matters:
Powder coating has become the go-to solution for parts exposed to mechanical wear, impact, and environmental damage. Unlike liquid paint, it delivers a thick, uniform layer without runs or drips, offering excellent durability and visual appeal.
Key advantages:
- Superior resistance to corrosion and chipping
- Eco-friendly process (no VOCs or hazardous waste)
- Available in a variety of textures and colors
- Long-term protection with minimal maintenance
At SAR Coatings, we operate fully automated powder lines designed for high-volume throughput without compromising on coating consistency or quality.
2. Zinc Flake Coating: When Corrosion Protection is Non-Negotiable
Ideal for: Fasteners, brake system parts, fuel system components, clamps, bolts
Zinc flake coating is engineered for extreme anti-corrosion performance, especially for small components exposed to salt spray, heat, and pressure. It's the industry standard in securing high-tensile fasteners—without the risk of hydrogen embrittlement.
What makes it essential:
- 720–1000+ hours of salt spray resistance
- Thin-film application (8–12 μm) for tolerance-sensitive parts
- Meets international automotive specifications (DIN, ISO, OEM standards)
- No heat curing required—safer for sensitive parts
SAR Coatings’ zinc flake system ensures complete coverage on threaded and recessed components through dip-spin and spray technologies—every fastener is protected, every time.
3. Zinc Nickel Plating: Precision Meets High Performance
Best suited for: Transmission parts, clutch systems, engine brackets, fuel rails
Zinc Nickel (Zn-Ni) plating provides a high-performance alternative to standard zinc, especially where components must tolerate high heat, aggressive environments, or complex geometries.
Why manufacturers trust it:
- Up to 1000+ hours of corrosion resistance
- Excellent adhesion and uniform thickness
- Outstanding chemical resistance
- Can be combined with post-treatment topcoats for extra durability
Our in-house plating systems at SAR Coatings deliver precisely controlled deposition, ensuring even the most intricate parts are coated without dimensional distortion.
4. Hybrid Coatings: Custom Protection for Complex Needs
Applications: Mixed metal parts, powertrain components, battery casings, assemblies
Sometimes, one type of coating isn’t enough. Hybrid coatings combine organic and inorganic technologies to create a multi-layered defense system tailored for specific stresses.
Performance benefits:
- Dual protection: chemical + corrosion resistance
- Enhanced bonding strength on multiple substrates
- Custom-engineered electric, hybrid, and commercial vehicle parts
- Flexible finish options for unique OEM requirements
At SAR Coatings, we don’t offer off-the-shelf solutions—we engineer hybrid coating systems that align with the functional and regulatory goals of your product.
5. Liquid Painting: Beauty That Lasts in Harsh Conditions
Common use: Exterior trim, interior panels, mirror housings, aesthetic parts
While functional coatings focus on protection, liquid painting balances form and function. For visible parts that define the look and feel of a vehicle, liquid coatings provide the precision, color fidelity, and finish flexibility required.
Advantages:
- UV, scratch, and chemical resistance
- Excellent leveling and surface flow
- Infinite customization for color, gloss, and texture
- Works well with plastic, composites, and metal
With SAR Coatings’ precision spray booths and skilled technicians, we ensure every painted part reflects the level of quality your brand stands for.
Why SAR Coatings is the Trusted Partner for the Automotive Industry
From two-wheelers to heavy commercial vehicles, SAR Coatings delivers engineered coating systems that improve product performance, reduce warranty claims, and meet demanding global standards.
What sets us apart:
- ISO-compliant coating facilities
- End-to-end in-house quality checks
- Process traceability and reporting
- Custom R&D support for OEM projects
- Flexible batch sizes and fast turnaround
Whether you need 500 precision fasteners coated or 50,000 brake parts plated, our systems scale to your production needs, without compromising quality or delivery timelines.
Final Word: The Right Coating Is an Engineering Decision
In 2025, choosing the right coating isn’t just about compliance—it’s about competitive advantage. Coated parts perform better, last longer, and create trust, both in your product and your brand.
With SAR Coatings, you're not just getting a service—you're gaining a coatings partner who understands the demands of modern manufacturing.
Let's Discuss Your Coating Requirements
Have a project in mind? Need help choosing the right coating for a new part? We’d love to hear from you.
Call: +91-9311813406
Email: info@sarcoatings.com
🌐Visit: www.sarcoatings.com