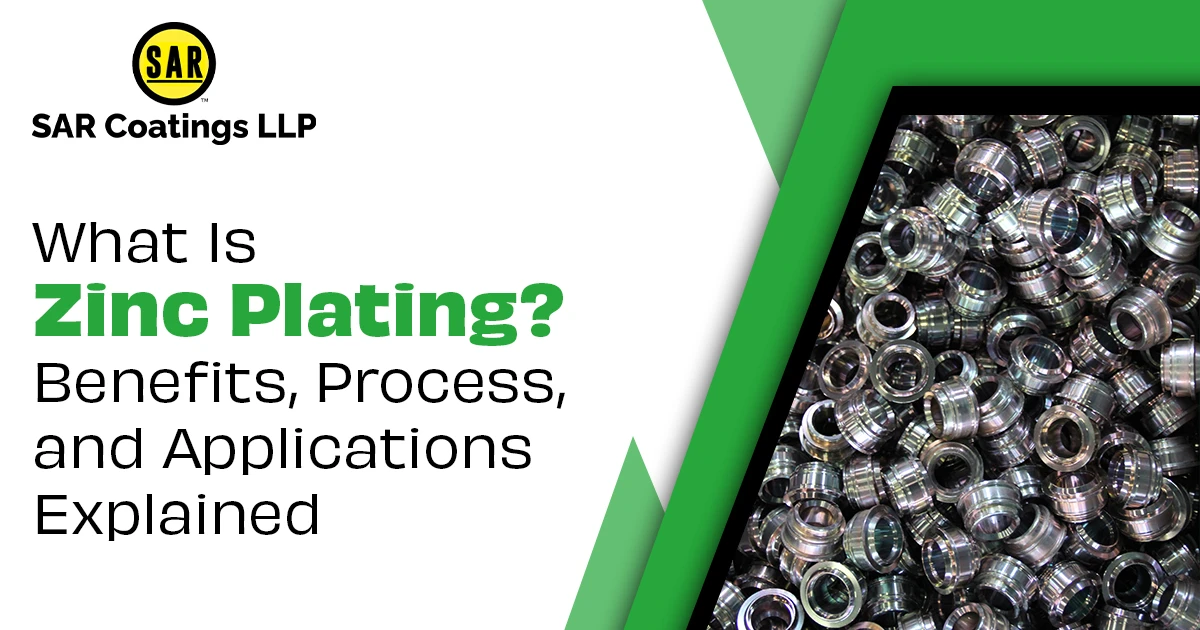
What is Zinc Plating? Advantages, process, and programs explained
Walk into any factory floor, open a toolbox, or look at the nuts and bolts of an automobile, and you’ll probably find one thing in not unusual: zinc-plated components. Zinc plating may not be a glamorous concern; however, in the world of metal manufacturing and business safety, it’s a silent workhorse. In case you're curious approximately what zinc plating is, the way it works, and why it's used across industries, this blog is your whole guide.
Permit’s dive into the sensible international of zinc plating—without the jargon and with simply sufficient depth to leave you knowledgeable, not overwhelmed.
What is Zinc Plating?
Zinc plating is a protective steel coating method in which a thin layer of zinc is applied to metallic or iron surfaces to prevent corrosion and rust. Think about it as a raincoat for steel components—it doesn’t replace the bottom material but adds a defense against the elements.
The idea is simple: iron and metallic materials, whilst exposed to moisture and air, oxidize and corrode over time. Zinc, being greater reactive, sacrifices itself to corrosion first. This sacrificial safety is known as galvanic protection—a chunk of technology that offers huge-time effects inside the actual international.
How does the Zinc Plating process work?
Zinc plating isn’t just about dipping metal into an answer and hoping for high-quality. It’s a carefully controlled electrochemical process that involves multiple steps:
1. Surface cleaning
Before something, the metal element needs to be very well cleaned. This consists of degreasing, acid pickling, or abrasive cleansing to eliminate oils, rust, and floor contaminants. Why? Because even a tiny spot of dust can save you from right plating adhesion.
2. Electrolytic bathtub
The wiped clean steel element is submerged in a tank containing a zinc salt solution (normally zinc sulfate or zinc chloride) and linked to a poor electric power rate (cathode). A zinc electrode is located in the bathtub and connected to a tremendous piece (anode).
3. Electroplating begins
While electricity flows through the answer, zinc ions travel and deposit onto the surface of the metal element. The thickness of the zinc coating may be managed by adjusting time, current density, and solution concentration.
4. Put up-Plating treatments
After plating, the element is rinsed, dried, and on occasion given a passivation layer or chromate coating to further beautify corrosion resistance and enhance the look (like yellow, blue, black finishes).
Types of Zinc Plating Finishes
Zinc coatings can now range not only in thickness but also in coloration and composition. Every type gives unique blessings:
Clean (Blue) Zinc: vivid, smooth end; decent corrosion resistance.
Yellow Zinc: consists of chromate; higher corrosion safety.
Black Zinc: decorative and practical; offers moderate resistance.
Zinc-Nickel or Zinc-Iron Alloys: Used for components wanting higher corrosion resistance, like inside the automobile or aerospace sectors.
Those finishes also impact the aesthetics and can affect how properly the component performs in harsh environments.
Key Benefits of Zinc Plating
Zinc plating has been a go-to method for over a century, and for a precise purpose. Here’s why industries continue to depend on it:
1. Top-notch Corrosion Resistance
Zinc acts as a sacrificial barrier, a defensive metallic element, even when the coating is scratched. It continues to guard uncovered regions through electrochemical reactions.
2. Value-powerful
In comparison to greater complex coatings (like chrome or stainless steel finishes), zinc plating gives an excellent return on investment. It’s lower priced, scalable, and dependable.
3. Good Adhesion and coverage
Zinc can be deposited uniformly over complex geometries—consisting of nuts, bolts, and fasteners—making it best for elements with threads, bends, and edges.
4. Stronger appearance
Whether it is the brilliant blue finish or matte black look, zinc coatings beautify the cultured appeal of industrial elements, which topics more than you would possibly assume in sectors like automobile, home hardware, or electronics.
5. Environmentally pleasant alternatives
Modern-day zinc plating has developed to conform to RoHS (limit of dangerous materials) policies. Trivalent chromates have in large part replaced harmful hexavalent options, making it greener and safer.
In Which Is Zinc Plating Used?
Zinc plating can be invisible to the untrained eye, but it's everywhere—from microwave ovens to grease rigs. Here are only some industries in which it plays a crucial function:
Automobile industry
Brake elements, chassis components, nuts, bolts
Protects from road salts and moisture
Domestic hardware
Door handles, latches, hinges
gives a smooth appearance and rust resistance
Electronics
Screws, enclosures, and brackets
Protects delicate electronics from moisture exposure
Production & Engineering
Structural fasteners and brackets
Prevents failure due to corrosion in harsh environments
Aerospace & defense
Specialised alloys like zinc-nickel for more advantageous durability
Critical in mission-critical, high-performance parts
Even your motorcycle chain or the zipper on a backpack is probably zinc-plated.
Zinc Plating vs. Different Coating Techniques
It’s critical to be aware that zinc plating isn’t the only recreation in town. Depending on the utility, it might compete with or complement:
Coating Type | Corrosion Resistance | Cost | Appearance | Ideal For |
Zinc Plating | Moderate to High | Low | Customizable | General-purpose hardware |
Hot-Dip Galvanizing | Very High | Higher | Matte grey | Outdoor/structural steel |
Powder Coating | High + Decorative | Moderate | Wide range | Consumer products, auto parts |
Zinc Flake Coating | Very High | Moderate | Uniform grey | Automotive & high-temp parts |
So why choose zinc plating? It’s the quality, stability of safety, price, and performance for small- to mid-sized components.
Commonplace questions about Zinc Plating
How long does zinc plating remaining?
That relies on the surroundings. In indoor settings, it may ultimate over 10–15 years. In coastal or relatively corrosive areas, extra coatings may be needed for extended lifespans.
Is zinc plating secure?
Sure, mainly with present-day trivalent chrome finishes. It’s widely utilized in food gadgets, electronics, and consumer goods.
Can zinc plating be removed or reapplied?
Yes. Through strategies like acid stripping, zinc may be removed, and the component can be recovered, though it’s regularly more cost-effective to replace low-priced gadgets.
Final Thoughts
Zinc plating won't be flashy, but it’s one of the maximum reliable and broadly used floor treatments in the commercial global. Whether or not you’re manufacturing car components, creation materials, or digital hardware, zinc plating gives you that an awful lot-wished safety in opposition to time, climate, and wear.
As industries grow greater traumatic and policies get tighter, zinc plating continues to adapt, with better green procedures, superior finishes, and smarter applications.
In case you're within the business of steel elements or production, understanding zinc plating isn’t just a nice-to-have—it’s critical.
Want zinc plating offerings or technical aid for your undertaking?
Connect with us at SAR Coatings—we’re here to help with reliable, enterprise-grade floor finishing answers.