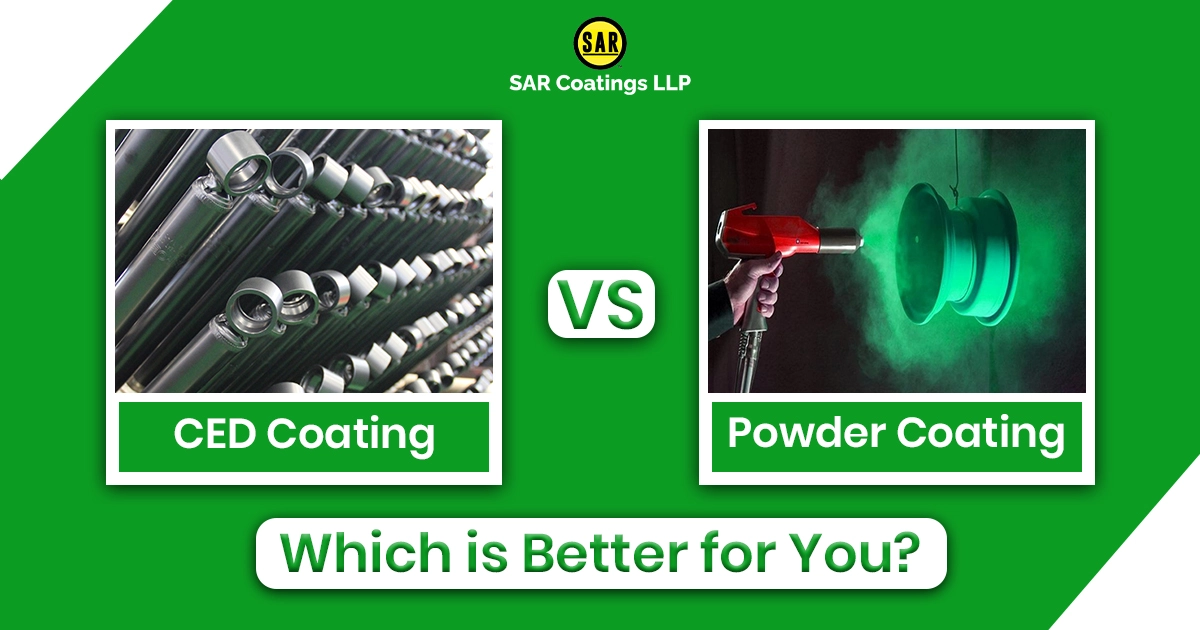
CED Coating vs Powder Coating: Which is Better for You?
When selecting a coating process for industrial or commercial applications, CED coating (Cathodic Electro Deposition) and powder coating are two popular technologies. Each offers distinct advantages depending on the project’s particular needs, such as corrosion resistance, aesthetics, cost, and environmental sustainability.
Understanding the differences between these two methods can help you make a better-informed decision. This guide will explore how each process works, its pros and cons, and which coating might be the better fit for your application.
Understanding CED Coating
Cathodic Electro Deposition, or CED coating, is a type of electrophoretic painting process that involves submerging a metal object in a water-based solution. An electric current is applied, causing paint particles to deposit uniformly on the surface of the object, which acts as the cathode.
This method is commonly used in industries where corrosion protection is a critical requirement. The automotive sector, for instance, uses CED coating for chassis, underbody parts, and other components that need long-lasting protection against rust and environmental damage.
Key Benefits of CED Coating:
- Exceptional corrosion resistance
- Even coating on complex geometries
- Water-based, low VOC emissions
- Long-lasting durability
Understanding Powder Coating
Powder coating is a dry finishing process where a fine powder made of resins and pigments is sprayed onto a surface using an electrostatic gun. The coated item is then cured in an oven, causing the powder to melt and form a solid, uniform layer.
Powder coating is favored in industries such as furniture, construction, consumer goods, and automotive finishing due to its appealing finish and wide color selection.
Key Benefits of Powder Coating:
- Broad range of colors and finishes
- Strong resistance to chipping and scratching
- Environmentally friendly (no solvents)
- Cost-effective and quick to apply
Comparing CED Coating and Powder Coating
Factor | CED Coating | Powder Coating |
Application Method | Electrochemical bath process with immersion | Electrostatic spraying and heat curing |
Durability | High corrosion and abrasion resistance | Great for abrasion, scratches, and wear, but less corrosion protection |
Aesthetic Options | Limited color range, typically matte finishes | Wide color palette with gloss, matte, satin, and textured finishes |
Environmental Impact | Water-based, low VOC emissions | Solvent-free, minimal waste, recyclable overspray |
Cost | Higher initial investment due to equipment and process | Generally more affordable, especially for smaller projects |
Surface Coverage | Excellent for complex shapes and hard-to-reach areas | May require skilled application on intricate parts |
Repairability | Difficult to repair without full recoating | Easier to touch up or recoat when damaged |
Trade-Offs and Considerations
- Durability vs Aesthetic Appeal
If your project demands maximum protection from corrosion, such as in outdoor environments or areas with high moisture exposure, CED coating provides excellent performance. It forms a consistent layer even on complex parts, ensuring thorough coverage.
On the other hand, powder coating offers a much broader selection of finishes and colors. It’s ideal for applications where visual appeal is a priority, such as consumer goods, decorative metalwork, and retail fixtures.
- Cost and Accessibility
Powder coating is typically more budget-friendly and accessible for small to mid-sized businesses. It requires less complex equipment and has lower setup costs.
CED coating, however, requires a larger upfront investment and more specialized facilities. Despite the higher initial cost, it may prove more economical in the long run for projects that need superior rust prevention and longer life cycles.
- Environmental Responsibility
Both coating processes are environmentally sound alternatives to traditional solvent-based paints. CED coating uses water-based solutions, reducing harmful emissions. Powder coating is also eco-friendly, emitting no VOCs and producing less waste—plus, overspray can often be recycled.
- Ease of Repair and Maintenance
One area where powder coating stands out is repairability. Damaged surfaces can be touched up with compatible powder materials. CED-coated parts are more difficult to repair, often requiring the entire surface to be stripped and reprocessed.
When Should You Choose CED Coating?
Consider using CED coating when:
- Corrosion resistance is a top priority.
- You’re working with complex parts that need even coverage.
- The component will be used in automotive or industrial environments.
- You need a long-lasting, reliable finish for high-performance use.
When Is Powder Coating the Better Option?
Powder coating is an excellent choice if:
- You want an aesthetically pleasing, colorful finish.
- The coating will be exposed to daily wear but not extreme weather.
- Cost and turnaround time are important factors.
- You require flexibility in design and appearance.
Final Thoughts
Ultimately, the choice between CED coating and powder coating depends on the needs of your project. CED coating provides unmatched corrosion protection, making it ideal for heavy-duty applications in industries like automotive and infrastructure. Powder coating, in contrast, offers more flexibility in appearance and cost, making it the go-to solution for decorative and consumer-facing products.
Before making a decision, assess the environmental conditions, performance expectations, and visual requirements of your project. If possible, consult with a coatings expert who can recommend the best solution based on your specific application.
Frequently Asked Questions
Q1 What's CED coating?
Ans. CED coating, or Cathodic Electro Deposition, is a type of oil process where an electric current is used to unevenly apply a defensive subcaste of makeup to the surface. The essence acts as the cathode in a water-grounded result containing epoxy resin and colors. This system ensures strong erosion resistance and is generally used in the automotive and artificial sectors.
Q2 What's the full quality of CED?
Ans. CED stands for Cathodic Electrodeposition. It’s also known as E-coating or Electrophoretic Deposition( EPD). This coating technology is extensively used for its capability to apply a truly rust-resistant substrate on essential shells, making it a favored choice in automotive and heavy industry manufacturing.
Q3 What's CED material?
Ans. In the environment of coating," CED material" refers to the water-grounded manual makeup used in the CED process. It substantially consists of epoxy resin and colors that are electrically charged and deposited onto essence shells. This eco-friendly manual is extensively used in auto manufacturing and other industries for its excellent erosion protection.
Q4 What's the difference between CED coating and powder coating?
Ans. The main difference lies in the operating system and face content. CED coating uses an electric current to deposit makeup in a liquid bath, which ensures invariant content, indeed on complex shapes. Powder coating, on the other hand, involves scattering dry powder onto a surface and curing it with heat. While Powder coating offers further color options and a thicker finish, CED coating excels in erosion protection and perfection.
Q5 What does powder coating do?
A powder coating creates a strong, smooth, and visually appealing finish on essence shells. It's further durable than traditional liquid makeup and offers excellent resistance to chips, scrapes, UV rays, humidity, and harsh rainfall. This makes it a popular choice for everything from ménage appliances to automotive corridors.
Q6 What's powder coating?
Ans. Powder coating is a dry finishing process where a fine powder made of resin and colors is electrostatically applied to a surface and then cured with heat. The result is a smooth, durable, and long-lasting finish that resists scrapes, erosion, and fading.
Q7 What are the advantages of powder coating?
Ans. Powder coating offers several benefits, including
- Superior continuity and erosion resistance
- A wide range of colors and textures
- Environmentally friendly( no dangerous detergents or VOCs)
- Cost-effective with minimum material waste
Q8 Where is powder coating generally used?
Ans. Powder coating is extensively used in industries similar to
- Automotive( skirtings, frames, machine corridor)
- Appliances( refrigerators, washing machines)
- Furniture( essence chairpersons, tables)
- Architecture( doors, windows, rails)
Q9 How long does powder coating last?
Ans. With proper surface and operation, powder coating can last 15 – 20 times or further. Its life depends on the terrain and exposure to elements like UV light and humidity.
Q10 Is Powder Coating environmentally friendly?
Ans. Yes, Powder coating is considered eco-friendly. It does not use dangerous detergents, produces little to no VOCs(volatile organic compounds), and redundant powder can frequently be reclaimed.