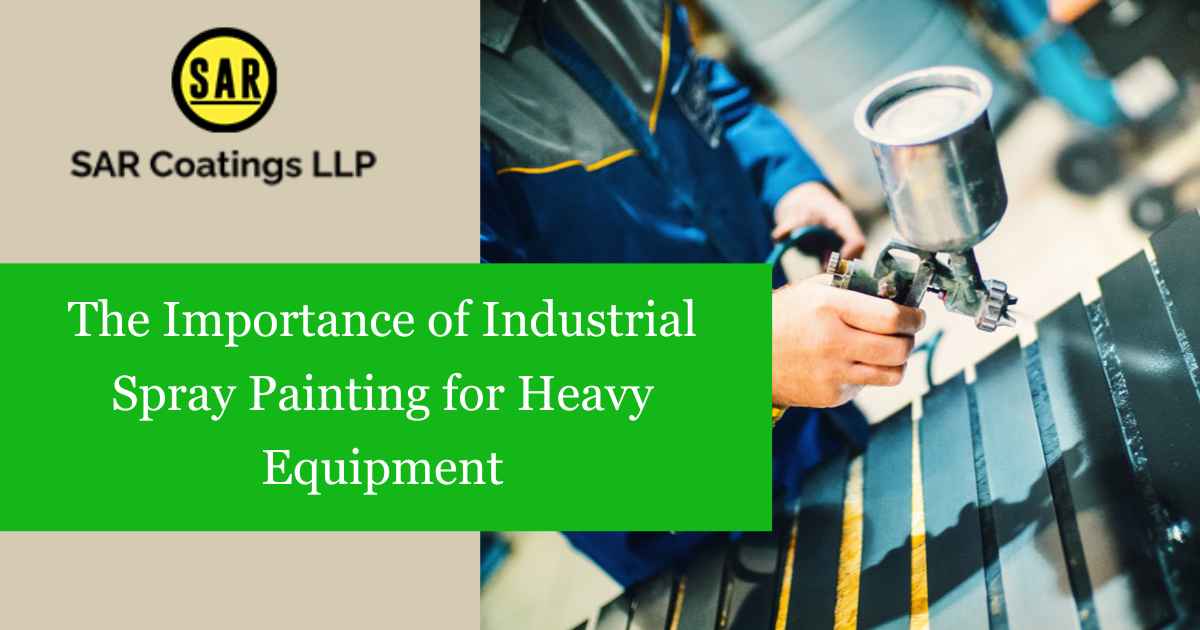
The Importance of Industrial Spray Painting for Heavy Equipment
At first glance, industrial spray painting may not appear as an art form, but it demands a level of skill and expertise that rivals that of the finest artists. It's a craft that works with various liquid materials, including paints, stains, and primers, to transform heavy equipment into more than just machines. The benefits of industrial spray painting extend far beyond aesthetics, offering unparalleled control and a flawless finish on a wide array of surfaces.
Why Does Heavy Machinery Need Industrial Spray Painting?
Many individuals and companies turn to experts like SAR Coatings for industrial or commercial spray painting services for their heavy machinery. But what drives this demand? The primary objective is to safeguard these colossal machines from rust and maintain their appearance, eliminating the risk of old paint chips contaminating the products they handle.
Industrial spray painting techniques are carefully tailored to protect the underlying materials, shielding them from the natural wear and tear that heavy equipment inevitably faces. The choice of coatings can vary based on the equipment and materials involved, with popular options including epoxy, urethane, and Line X paints.
How Is Industrial Spray Painting Done?
To ensure the success of an industrial spray painting project, meticulous preparation is essential. Whether the equipment is made of steel or has undergone sandblasting, the surface must be free from rust, debris, or stains. Any imperfections in the surface can cause the paint to fail to adhere properly, leading to premature peeling.
The process typically begins with a high-pressure wash using specialized equipment, effectively cleaning the surface and preparing it for painting. Following this, a primer is applied to facilitate paint adhesion and create a smooth finish. Once the primer has set, the industrial spray painting process can commence. The final step involves applying a top coat, providing added protection against environmental elements and further reducing the risk of rust.
Key Considerations in Industrial Spray Painting
Industrial spray painters are not mere technicians; they are artisans in their own right. They carefully consider various factors to ensure a flawless finish. Here are some critical aspects they focus on:
Substrate Preparation
Preparing the surface for painting is a pivotal step. Industrial spray painters must ensure that the substrate is impeccably cleaned, as nearly 80% of painting failures can be traced back to inadequate surface preparation.
Paint Thinning
Paint sometimes needs thinning for proper application and coverage. The choice of thinners can vary depending on the type of paint being used. While mineral spirits are suitable for most paints, others may require different thinners.
Spraying
Achieving the desired metal finishing requires precise spraying techniques. Factors such as the type of finish, paint type, and substrate material come into play. Industrial painters have a wide array of spraying devices and guns at their disposal, allowing them to customize the painting process to meet specific requirements.
Commercial Spray Painting Methods
Different industrial spray painting methods offer distinct advantages and disadvantages. Airless sprayers, for instance, provide greater control over the finish and reduce paint waste by recirculating excess paint. Here's a breakdown of a few industrial spray painting methods:
Air Gun Spraying
Air gun spraying is ideal for delicate work, including lacquers, paints, varnishes, shellac, and other finishes. It utilizes air and fluid compression for atomization, ensuring even application.
Electrostatic Spray Painting
This modern technique, widely used in the automotive sector, ensures even coverage on various surfaces, including metals, doors, windows, railings, and metal fencing. Specialized equipment such as air-assist guns and HVLP sprayers is employed.
HVLP (High Volume Low Pressure)
HVLP spray painting relies on turbines and heat to stabilize paint, reducing atmospheric condensation and improving adhesion. This method is suited for glossy, smooth-textured coatings.
LVLP (Low Volume Low-Pressure)
LVLP spray painting utilizes less air volume and lower air pressure compared to HVLP. It can still achieve a transfer efficiency of 65% or better.
Airless Spray Guns
This technique involves pushing paint through a nozzle via a hose, eliminating the need for compression. It's ideal for glossy, glass-smooth-textured coatings.
Liquid Painting at SAR Coatings
SAR Coatings stands as a testament to the art of industrial liquid painting. They continually invest in high-quality machinery to meet customer demands. We excel at providing high-quality painted finishes that meet exacting standards. They offer specialized coatings, enhancing insulative or conductive properties using electrostatic spray, fluid bath, or heat shrink processes. Furthermore, our team also conducts rigorous testing of finishes, including gloss level, coating thickness, adhesion strength, porosity, colour shade, dielectric strength, and insulative or conductive properties.
If you're interested in discussing your industrial spray painting requirements, don't hesitate to contact SAR Coatings today. For more captivating articles on manufacturing and technology, explore our blog.